Polysilicon solutions
Customized based on site conditions
1. On-site technical data (provided by the client), for example:
Serial Number |
Project |
Unit |
Value |
1 |
Number of 40-rod reduction furnaces |
Units |
10 |
2 |
Height of silicon core/rod |
mm |
3000 |
3 |
Length of silicon core/rod beam |
mm |
260 |
4 |
Length of a pair of "Π-shaped" silicon cores/rods |
mm |
5600 |
5 |
Silicon core diameter |
mm |
15*15 square silicon core |
6 |
Electrode spacing |
mm |
230 |
7 |
Target diameter of silicon rod |
mm |
180-200 |
8 |
Operating pressure inside the furnace |
MPa |
0.8 |
9 |
Maximum operating voltage of the electrode |
kV |
12 |
10 |
Altitude |
m |
1500 |
2. Grouping of silicon cores/rods in the reduction furnace
The silicon cores/rods of the 40-rod reduction furnace correspond to the A, B, and C phases of the reduction transformer, with the following correspondence:
A1: 8 pairs of rods, A2: 6 pairs of rods;
B1: 8 pairs of rods, B2: 4 pairs of rods;
C1: 8 pairs of rods, C2: 6 pairs of rods.
3. Electrical system structure of the reduction furnace
The entire electrical system consists of core equipment composed of voltage regulating power cabinets, voltage regulating control cabinets, and computer operation management systems produced by our company, as well as peripheral equipment composed of reduction transformers produced by professional transformer manufacturers. The pressure-reducing transformers and high-voltage switches are inside the voltage regulating power cabinet. Among them, the computer operation management system is a centralized public device that is independent of the number of reduction furnaces.
4. Regulator design
(1) Design principle: The current setting for the outer, middle, and inner silicon rods is independently set and not mixed in series, so that the temperature of the outer, middle, and inner silicon rods can be adjusted independently.
A three-phase balanced power supply method is adopted, and each phase of the transformer supplies power to 12 or 14 pairs of rods (60 pairs of rods supply power to 20 pairs of rods for each phase).
(2) Selected scheme: For example, 6 reduction power supply cabinets are shared by each 40-rod reduction furnace to control 40 pairs of rods, and each reduction power supply cabinet adopts a structure that is first independent and then series, powered by transformer phases A1, A2, B1, B2, C1, and C2. In summary, this control method considers both the uniform temperature field issue and satisfies the three-phase balanced power supply of the transformer. The distribution of reduction power supply cabinets per furnace is shown in Table 1: Reduction Power Supply Cabinet Design:
Table 1: Reduction Power Supply Cabinet Design
Transformer tap number |
Reduction power supply cabinet |
Load |
Control method |
A1 |
Reduction power supply cabinet |
8 pairs of silicon cores |
First independent, then series |
A2 |
Reduction power supply cabinet |
6 pairs of silicon cores |
First independent, then series |
B1 |
Reduction power supply cabinet |
8 pairs of silicon cores |
First independent, then series |
B2 |
Reduction power supply cabinet |
4 pairs of silicon cores |
Series |
C1 |
Reduction power supply cabinet |
8 pairs of silicon cores |
First independent, then series |
C2 |
Reduction power supply cabinet |
6 pairs of silicon cores |
First independent, then series |
(3) Starting scheme: The high-voltage starting power supply provides an adjustable voltage of 0~12KV to break down the silicon core, and each furnace and each phase is independently pressurized. The method of breaking down one group and then another group is adopted to maintain the reduction power supply until all of them in this phase are broken down; the starting power supply automatically enters constant current operation.
For the silicon core start-up of the 40-rod reduction furnace in this project, there are three start-up modes, which are described as follows:
Start-up mode one: One-by-one start-up (the 1st and 2nd pairs of rods), high-voltage start-up begins, the resistivity of the silicon core is large, so a one-by-one breakdown method is used.
Start-up mode two: One-by-one or one-by-two start-up (the 3rd and 4th pairs of rods), two methods are selectable (simultaneously available).
Start-up mode three: One-by-four start-up (the 5th to 8th pairs of rods), when 9 power cabinets start running at the same time, at this time, 36 pairs have already been broken down individually, the temperature inside the reduction furnace is already very high, and the resistivity of the silicon core becomes smaller. In order to improve work efficiency, a one-by-four breakdown method can be used at this time.
5. Voltage regulating control cabinet
One reduction power supply control cabinet per furnace is responsible for the start and stop, communication, and fault protection of the reduction power supply cabinet.
The reduction power supply control cabinet has three main functions: issuing trigger adjustment commands to the power cabinet, performing electronic comprehensive protection on the power cabinet, and connecting the communication between the power cabinet and the host computer.
6. Grounding cabinet
Built-in multi-channel wall collision detection equipment, used to detect grounding faults of silicon rods in the furnace.
7. Computer operating system design
The microcomputer monitoring system without operating switches adopts a dual-server redundancy method and fiber optic communication method, and can be shared by multiple furnaces. The two servers are in a hot standby state; if one server has a problem, the other server automatically starts running.
Beijing YiNeng Electric Technology Co., Ltd.
Address: No.27, Keyuan Road, Daxing District, Beijing
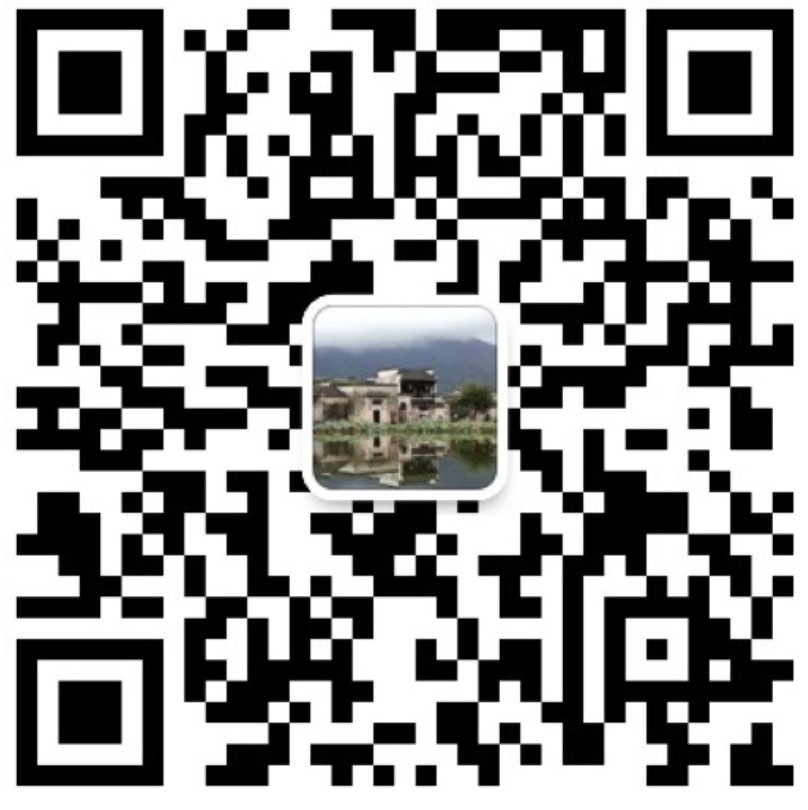
Copyright©Beijing YiNeng Electric Technology Co., Ltd.